haped cutters are not new to the industry. They were introduced decades ago when drilling environments began to change and more complex formations introduced new challenges, and they have been part of drill-bit technology portfolios since the 1990s. For many years, development teams have been investigating downhole conditions that were causing cutter damage and drilling dysfunctions, continually playing with the balance between materials and geometry.
That knowledge has been a springboard for focused R&D efforts to improve cutter designs to contend with demanding drilling conditions and more complex wellbores. Today, shaped cutters push performance to new limits in applications that traverse multiple formations on a single run, from interbedded, to hard rock and abrasive formations, through sand, clay, sandstone, and limestone. Unitooth& Side Tooth
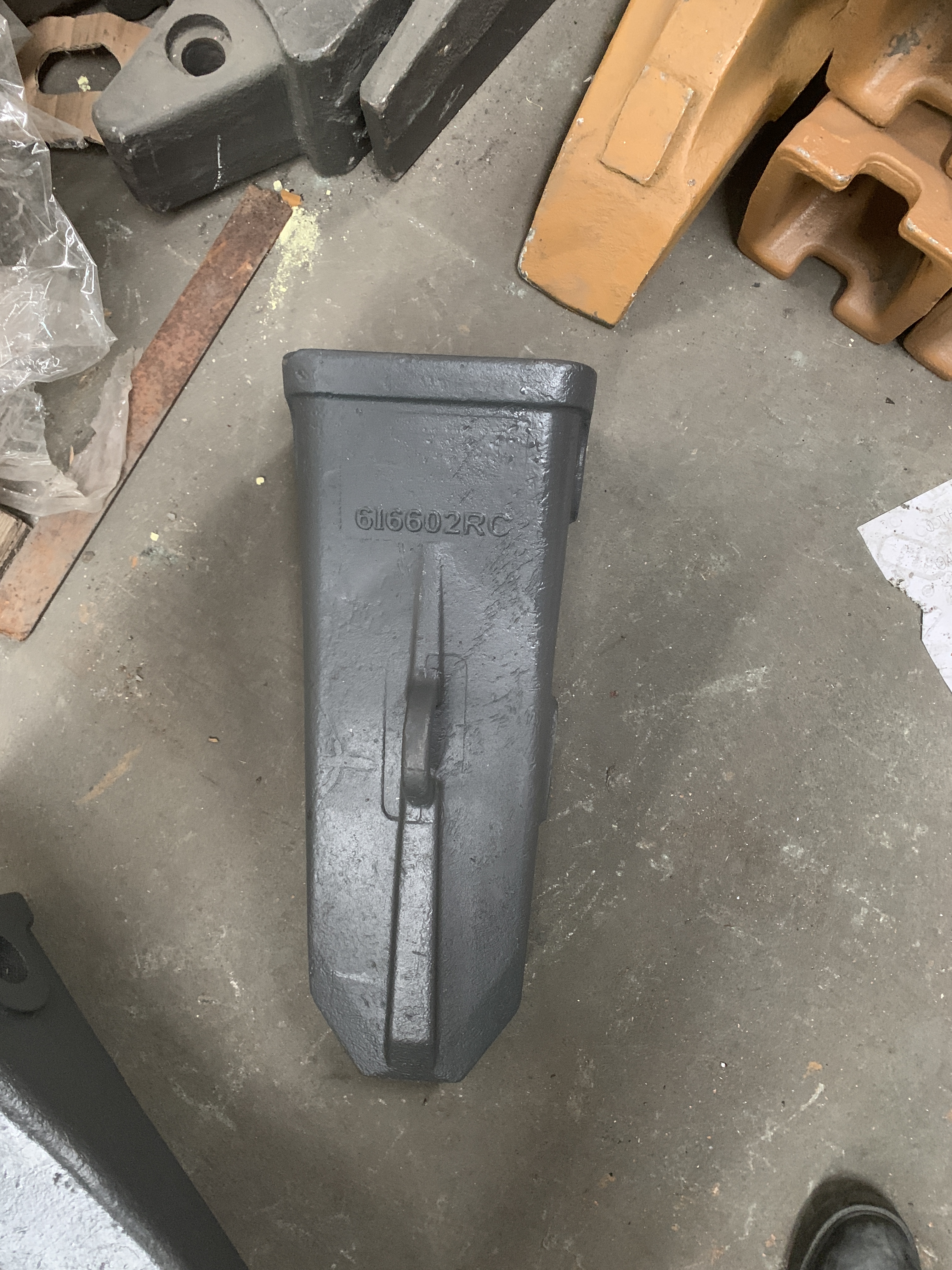
An entire suite of shaped cutters (Fig. 1) has been developed using the latest in materials research to address a range of challenging formation types and applications. Drilling engineers can place combinations of specialized cutters on a single bit to drill efficiently through complex formations.
One of the advanced cutters (Fig. 1a) that emerged from these development efforts is a design that improves performance in hard formations. The resulting cutter has novel edge geometry to stand up to high-impact loads and a secondary chamfer on the diamond face that enables it to withstand higher loads than polycrystalline diamond compact (PDC) cutters. This allows it to maintain drilling efficiency in hard, interbedded formations, leading to a higher overall rate of penetration (ROP) for the interval.
When drilling in hard, abrasive formations, heat generated from the rock-cutter interaction can break down the integrity of the cutter, leading to premature wear and reduced performance. Engineers focused on enhancing the improved cutter tip to develop a cutter (Fig. 1b) that remains cool in hard, abrasive formations and is particularly effective in sandstone, where it exhibits considerably less microfracturing and wear than traditional cutters.
Complex runs often mean that bits must drill through very different formations, from interbedded, hard rock to more abrasive formations. To contend with these varying conditions, a cutter must be effective in high-impact loading conditions and still be functional at end of run. Another specialized cutter (Fig. 1c) was developed to deliver this balanced performance, reducing friction and heat generation at cutter/rock interface, breaking up rock cuttings, and enabling faster drilling and longer runs with a lower weight on bit (WOB) requirement for a given ROP.
Conditions where point loading is required, such as drilling through evaporites or high-mud-weight environments and in drilling runs where WOB is limited, require a cutter with the ability to distribute more weight to a smaller portion of the rock. Baker Hughes designed a cutter (Fig. 1d) for these conditions that penetrates the formation more effectively than standard cutters by generating a larger depth of cut using the energy available to deliver faster drilling runs.
The most recent addition (Fig. 1e) to the specialized cutter portfolio takes on even more demanding conditions with a design that delivers greater durability with the inclusion of secondary chamfering, a relief in the center of the cutter, and enhanced point-loading capability.
All these specialized cutters share the goal of improving ROP, extending bit life, and making longer drilling runs possible, and each design has specific application and performance characteristics that improve drilling efficiency. But optimizing the placement of these shaped cutters on the drill bit is not easy. There are many interrelated variables, so determining what to change to improve performance is a formidable challenge. Finding the best path forward means identifying the right tools for the job, and often, that means not just one cutter, but multiple cutter types positioned appropriately on the correct part of the bit.
Costs associated with drilling constitute 30–40% of total well costs for onshore drilling programs, so finding ways to improve the process can significantly affect the bottom line. In a conventional drilling program being executed in Northeast British Columbia, Canada, the challenge was finding a way to drill effectively through interbedded lithology with hard rock and highly abrasive formations that were causing excessive vibration and frequent cutter breakage in offset wells.
A computer simulation of the downhole environment led to a practical solution, using a 6¾-in. Dynamus extended-life PDC bit fitted with two types of specialty cutters to resolve the drilling challenges. The ShockWave cutter provided the durability to drill efficiently in interbedded formations, eliminating issues with thermal damage and cutter chipping, while Apex cutters addressed issues with wear, providing backup as the primary cutters wore down and allowing drilling to progress without a drop in ROP.
This combination of shaped cutters saved 26 hours of drilling time by eliminating one planned run to change the bit and delivered a 76% meterage improvement over the pad average.
Conventional drilling poses one set of challenges, while drilling in shales presents another. For an operator executing a drilling program in the Vaca Muerta Shale in Argentina, the issue was a long, slimhole horizontal well where high-weight transfer was causing premature bottomhole assembly failures, and limited power input from rig systems was restricting penetration rates in the offset wells.
Experts carried out advanced simulation modeling to identify the combination of bit and specialty cutters to best address the high-weight transfer issue and improve ROP. They determined that using Prism cutters on a 6¾-in. extended-life PDC bit would increase ROP in the long, shale lateral section. With the Prism cutters judiciously placed on the bit, the operator was able to safely increase WOB to increase ROP without risking tool damage. Combining the specialty cutter with the AutoTrak automated reservoir navigation drilling system yielded a 13% improvement in ROP vs. average offsets in a single lateral section run, with the best run in the drilling program delivering 29% better ROP (Fig. 2).
Suboptimal drilling is always detrimental to operations, but in deep water, where drilling comprises approximately 60% of total well drilling and completion costs, inefficiencies are particularly costly. This was a significant driver for an operator drilling in the Caribbean where a complicated deepwater build section through clays and sandstones presented tough, interbedded carbonate stringers that made it difficult to achieve the desired build rates without applying excessive steering forces. The bit was encountering excessive vibration and experiencing stick/slip in the offset wells.
Simulation modeling allowed drilling engineers to identify the bit/shaped-cutter combination that would deliver precise steering control and better bit stability. Simulation results led to the decision to use a 12¼-in. extended-life PDC bit fitted with two specialty cutters. The point loading of the Apex cutter enabled penetration of the ductile formation with lower WOB, and the StabilisX cutter improved torsional stability to cut through the hard formation. Placing this combination of cutters on the bit and using the AutoTrak automated reservoir navigation drilling system improved ROP by 30% and reduced stick/slip by 80% and at the same time extended bit life and increased the length of the drilling runs.
Advanced shaped-cutter technology delivers a range of performance improvements in demanding drilling environments, but this is not the end of the journey. The use of sophisticated simulation software to truly understand the demands of the formation and how each cutter will perform with a particular placement on the bit is helping engineers resolve current drilling challenges and at the same time improve and refine both the cutters and the drilling process.
Results from more than 50,000 runs where shaped cutters resolved drilling issues demonstrate that by matching the combination of cutters to the formation and the downhole conditions, it is possible to improve ROP, extend bit life, and drill longer runs for more cost-efficient operations.
The performance of these cutters combined with enhanced modeling capabilities also establishes a track record of reliability, and as drilling environments evolve, ongoing investment in shaped-cutter development will continue to advance technology to ensure drillers have the right tools for the job.
Since joining Baker Hughes in 2007, Derek Nelms has served in a variety of drill-bit design, drilling engineering, and technology sales roles. He holds a BS in mechanical engineering from Texas A&M University.
The Journal of Petroleum Technology, the Society of Petroleum Engineers’ flagship magazine, presents authoritative briefs and features on technology advancements in exploration and production, oil and gas industry issues, and news about SPE and its members.
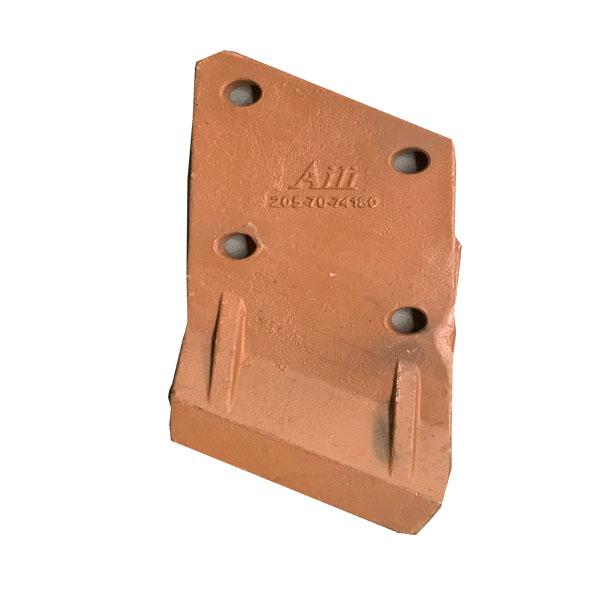
Forging bucket tooth ISSN: 1944-978X (Online) ISSN: 0149-2136 (Print)