You have successfully submitted your enquiry. Someone from our company will respond ASAP
As the leading global fender manufacturer, ShibataFenderTeam (SFT) has over 60 years of experience in delivering high-quality fender systems that safeguard people, vessels, and infrastructure alike. The company is committed to excellence and provides unparalleled technical expertise, consulting, engineering, manufacturing, testing, and after-sales services for the shipping industry. Boat Airbag

ShibataFenderTeam takes immense pride in its global presence, which makes its professional contacts easily accessible to a wide range of clients. Customers rely on personalised consulting services and direct exchanges, which are facilitated through the company’s flexible approach and extensive network. Through its offices and local agents, SFT stays closely connected with clients to provide comprehensive consultancy services. The company’s knowledgeable sales team and other agents are familiar with local conditions and regulations, creating a strong global network to deliver specially tailored solutions for each customer. Customised fender design and manufacturing for the shipping industry
In the maritime industry, it is widely acknowledged that no two projects are identical, and fender design concepts are rarely simple or off-the-shelf products. With this understanding, SFT advocates for a holistic approach to fender system design, where project conditions, components and design, and manufacturing are all viewed as equally important aspects of fender design and production. This approach helps to ensure the reliability and durability of the fenders, as well as extending optimal performance throughout a fender system’s complete service life.
ShibataFenderTeam prioritises the in-house manufacturing of safety-critical fender systems, ensuring the utmost quality and reliability at all its production facilities. The company has rubber fender manufacturing facilities in Malaysia and Japan, which are both equipped with state-of-the-art manufacturing and testing equipment. In addition, the company mixes its own rubber compound at a mixing plant in Malaysia using the latest compound mixers and associated technology. This provides increased production control and helps to establish the company as a pioneer of fender manufacturing. SPC Cone Fenders have an exceptionally good energy absorption to reaction force ratio and a high shear stability. CSS Cell Fenders are very robust and provide a good load distribution on substructures. We deliver Extruded Fenders in different shapes and as D or as Square Fenders. We deliver a wide variety of foam products, including Ocean Guard, Ocean Cushion, Submarine Foam Fenders, SSD Fenders, Donut Fenders, and Buoys. Pneumatic Fenders show a proportional increase of energy and reaction; built as per ISO 17357-1:2014 . Also available as Hydropneumatic Fenders. Low friction HD-PE Sliding Fenders are offered, as well as UHMW-PE Plates for steel panels. ShibataFenderTeam offers reliable and high abrasion-resistant Tug Boat Fenders for extreme conditions. Parallel Motion Fenders are highly customised systems, which eliminate a second ship/panel contact. A wide range of standard shapes, load ratings, materials, and anchor systems are available with strong and long-lasting designs.
Alongside its Malaysian and Japanese facilities, ShibataFenderTeam also has a production facility in Germany, which initially began producing HD-PE Sliding Fenders in 2014. Since then, it has expanded to produce steel panels for rubber fender systems, as well as foam fenders and buoys. Maritime mooring and berthing fenders
ShibataFenderTeam uses its expertise in working with rubber, steel, polyurethane, and polyethylene to create an extensive range of products that cater to all maritime mooring and berthing applications. Some of the products offered by the company include: Rubber fenders: high performance rubber fenders for use in areas with low variation in water level. Fixed fenders (all but cylindrical fenders) are mostly equipped with steel panels to allow for low hull pressure. Easy-to-install Conical Fenders (SPC Cone Fenders): offer a remarkable energy absorption to reaction force ratio and high shear stability, with no loss of performance up to a 10° approach angle. Hollow and lightweight Cell Fenders (CSS Cell Fenders): with easy assembly and installation, excellent shear force resistance, and cost-effectiveness, leading to optimal load distribution on the frontal panel and lighter panel construction. Fully molded Element Fenders with mounting plates: A modular and compact design and small footprint allow for easy installation. Good energy absorption to reaction force ratio (E/R). Energy-absorbent Cylindrical Fenders (FE Element Fenders): offer softer berthing and dimensions and features, such as pre-bending or jointing, can also be requested. V Fenders for turning dolphins and pivot points: available in different head widths and with optional steel plates for UHMW-PE frontal plates or a steel plate. Individually engineered Parallel Motion Fenders: custom-engineered systems typically equipped with Cone, Cell, or Element Fenders. Incorporates a turning lever arm that restrains panel movement solely in parallel with its mounting, regardless of impact level and angle. Custom-made Pile Fenders: provide a single point-of-contact between the vessel and the fender system at any water level. Foam Fenders: high-performance systems ideal for projects with fluctuating water levels, as well as ship-to-ship and ship-to-shore operations, and cruise terminals. Ocean Guard Fenders: with a foam core and tough polyurethane skin. These fenders have energy absorption, low hull pressure, non-marking skin, and low maintenance requirements. Ocean Cushion Fenders: supplied with a heavy duty chain and tire net. Extremely robust for heavy duty operations. Donut Fenders: designed to slip over a stationary monopile. The fender floats up and down with the fluctuating water levels and rotates. Submarine Foam Fenders: equipped with a counterweight to keep parts of the fender below the water line. Used for ship-to-shore and ship-to-submarine operations at navy berths, also suitable for operation in Arctic conditions. SSD Fenders: for quick and convenient handling on naval and commercial vessels. Ideal for limited storage. Pneumatic Fenders: An abrasion-resistant, air-filled rubber fender that is easily deflatable. Available as a special hydropneumatic version with submerged contact area for submarines.
Other available fender types include corner fender systems, as well as rolling, extruding, Komposite, and tugboat fenders. Polyethylene sliding plates and fenders are also available and are ideal for use with steel fender panels.
As well as fenders, SFT also offers buoys, barriers, bollards, fixings, and accessories. For specialised projects, the company also offers highly customised products, made from materials such as rubber and steel, for other fender and marine applications.
All SFT products are thoroughly tested to ensure they adhere to the latest industry standards. The company helps to support and promote the development of new industry guidelines and is part of PIANC Working Group 211, which helps to develop the ‘Guidelines for the design of fender systems’. As part of its comprehensive approach, SFT also offers after-sales services, including site assessments and personalised maintenance plans for maritime infrastructure.
The first part of the SFT White Paper Series on fender manufacturing outlines the considerations relevant to determining what makes a good fender.
ShibataFenderTeam's enhanced focus on in-house design and manufacturing helps it to offer customised fender solutions to protect people, ships, and port infrastructure.
This white paper contains further information about ShibataFenderTeam's consulting, manufacturing, engineering and after-sale services.
ShibataFenderTeam is a specialist in the design of safety-critical fender systems that protect people, ships and port infrastructure. We offer consulting, engineering, manufacturing, testing and after-sales service.
SFT channelled the power of fender systems for enhanced maritime safety and worked in collaboration with a renowned construction equipment firm.
The contractor awarded with this project entrusted ShibataFenderTeam with the design and supply of the fender systems for the new berth.
Sky Princess cruise ship is the fourth Royal-class Princess Cruises vessel.
ASD TUG 2913 is a new series of highly manoeuvrable and powerful azimuth stern drive (ASD) tugboats offered by Damen Shipyards Group.
The Balla Balla infrastructure project (BBIP) involves the construction of iron ore transportation infrastructure at the Balla Balla Port, including a 162km railway line connecting the facility to iron ore deposits in the region.
ALP Future Class is a series of four next-generation, long-distance towing and anchor handling tugs (AHTs).
The non-self-propelled vessels (NBL-91 project) are a series of 12 barges being built by NIBULON shipbuilding and repair yard, which is based in Ukraine.
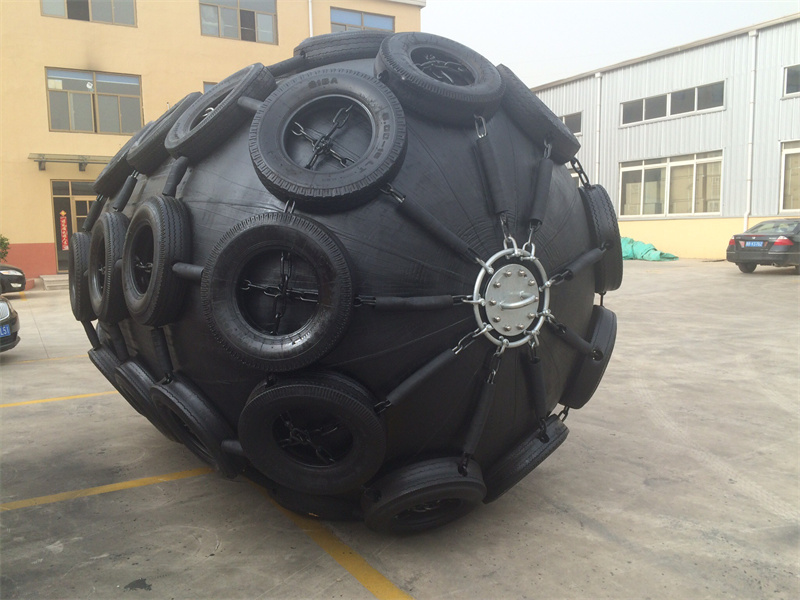
Inflatable Marine Airbags The leading site for news and procurement in the ship industry