What is the difference between brushed and brushless motors? One has brushes and the other not, right?
While on the surface this is, of course, true, the real question is why do both types exist? What are the main benefits and limitations of either? Use Of Electric Motor

Read on to find out.
RELATED: 10 OF THE MOST IMPORTANT INVENTIONS OF NIKOLA TESLA
But, before we get into comparing the two, it is useful to spend some time discussing each type of motor in isolation.
A brushed DC motor uses wound wire coils, called the armature, which act as a two-pole electromagnet. Twice per cycle, the current's directionality is reversed by the commutator, which is a mechanical rotary switch. The electromagnet’s poles pull and push against the permanent magnets along the outside of the motor. The commutator then reverses the polarity of the armature's electromagnet as its poles cross the permanent magnets' poles, to form a direct current.
Stay ahead of your peers in technology and engineering - The Blueprint
Brushed motors were the first commercially important motors, and have been used for well over 100 years to operate motors in commercial and industrial applications. They are the most basic and have been in use since the late-1800s.
Brushed motors can be varied in speed by changing the operating voltage or the strength of the magnetic field within them.
This level of control is very useful for many applications.
Brushed motors tend to consist of four basic components:
We'll discuss how these components work in conjunction with the next section.
As previously mentioned, a brushed motor consists of four basic components. The first, called the stator, generates a stationary magnetic field that surrounds the rotor.
Typical anatomy of a DB brushed motor.
Top left: The complete motor and casing.
Top right: (from left to right) the plastic cap with exposed brushes, the rotor with the commutator and electromagnetic windings, and the casing showing permanent magnets and stator inside.
Bottom left: The isolated rotor/armature assembly (commutator electromagnet windings, etc).
Bottom Right: Close up of plastic cap with brush electrodes.
Source: Ilia Krivoruk/Wikimedia Commons
This magnetic field is generated using two curved permanent magnets. These magnets are usually stationary (do not move), hence the term.
It is also important to note that one will have its North pole pointing towards the rotor, and the other its south pole toward the rotor.
The rotor, or armature, is made up of wire coils that can, when electricity is run through them, produce a magnetic field.
This is the part that moves (hence the name 'rotor') and turns the main shaft of the motor.
Through magnetic polar attraction, the rotor's magnetic field will attempt to align/repel with that of the stator, causing the rotor to spin about its axis.
When electricity is run to the motor a magnetic field is generated that attracts (and repels against) the fixed magnets in the stator. In order to keep the rotor spinning, the magnetic field needs to be reversed every 180-degree turn of the rotor (in a simple single-armature brushed motor).
This change in rotor magnetic polarity is performed by the motor's brushes (usually made of carbon) and a commutator (the part that "commutes" or reverses the electrical current to the rotor's armature. The brushes are usually just two fixed electrodes that rub against the commutator ring as it spins with the rotor.
The brushes will also tend to be spring-loaded to ensure they remain in contact with the commutator.
The commutator usually consists of a small, usually copper, cylinder attached to the rotor with breaks at regular intervals (e,g, 180 degrees in a single armature rotor). Electrical current will flow through one half of the commutator, through the armature, and back out of the other half of the commutator.
As the rotor (armature) spins, the also commutator spins, constantly making and breaking an electrical circuit with the brushes. This causes the magnetic poles of the rotor's windings to flip magnetic polarity as the circuit is broken in one direction and reconnected in the other -- i.e. the current is reversing every 180-degrees.
More complex motors will have a series of armatures with breaks between them on the commutator. This helps prevent potential seizing of the motor if the brushes complete a circuit across the commutator gaps.
In other words, each armature loop takes it in turns to become an electromagnet and attract/repel against the outer fixed stator permanent magnets. Pretty neat.
In real motors, armatures will also consist of a mass of wires instead of a single wire. This helps greatly improve the strength of the electromagnet and therefore the torque of the motor.
Typically, brushed DC motors are housed in a pressed steel and zinc coated housing with a plastic cap on one end. The housing and cap will usually have a series of holes that are generally present to allow airflow through the motor to help prevent overheating.
There are also usually screw holes too for mounting the motor in place. The plastic cap will also hold a pair of connection pins for connecting the power supply and preventing shorting through contact with the metal motor housing.
If you are having trouble visualizing how a DC brushed motor works, here is a great simulation.
Brushed DC motors (BLDC) can be found pretty much everywhere in your home and while you are out and about. Whenever a means of converting electricity into rotational motion is required, chances are you will find a brushed DC motor.
In your home, any toy or electronic device that moves will likely have one. Electric toothbrushes, motorized bread slicers, your child's favorite RC car, will all take advantage of these amazing pieces of engineering.
In the wider world, DC brushed motors are still widely used today in machines such as electric propulsion systems, cranes, drills , and steel rolling mills, to name but a few, because of the ability to alter the torque to speed ratio, which is exclusive to brushed motors
As opposed to brushed DC motors, and as the name suggests, brushless DC motors do away with the need for brush electrodes to turn the rotor. They also remove the need for a physical commutator.
Also known as electronically commutated motors (ECM or EC motors), they are widely considered to have a higher power-to-weight ratio, speed, level of control, and lower maintenance requirements when compared to brushed motors.
They also reverse, in part, the working principles of the brushed motor. For example, permanent magnets are used on the rotor while controllable electromagnets are used to spin the rotor.
Brushless motors typically come in two forms:
In a brushless motor, the copper winding coils are fixed, as it is the permanent magnet that turns with the rotor. A small circuit board is used to mimic the job of brushes in a conventional brushed motor by managing the energy supply to the electromagnets.
Other than that, the basic principle of the technology is the same as a brushed motor, although the application is slightly different. Brushless motors first appeared during the 1960s, thanks to the advent of solid-state electronics.
We have already gone over, in-depth, how a brushed motor works. A brushless motor, as previously suggested, works in a similar fashion with the exception of which parts are fixed and which parts turn.
The electrical current is not supplied to the rotor at all, and the permanent magnets are attached to the shaft, not the stator. The electromagnet coils are fixed in place on the stator and, as such, there is no longer any need for brush electrodes and a commutator.
As in brushed electromagnet coils, the coils here usually consist of a soft iron core wrapped in wires.
The fixed electromagnet coils are progressively turned on and off in sequence, to temporarily magnetize them to either repel or attract the permanent magnets on the rotor. They, in effect, use magnetism to push and pull the magnets attached to the rotor, to affect a spin of the shaft.
In this fashion, torque is generated by keeping the magnetic fields of the rotor and stator constantly misaligned. As the permanent magnets attempt to align, the motor's control system automatically either turns off or changes the polarity of the electromagnets to maintain the misalignment of fields.
This is achieved through the use of sensors that are able to detect the angle of the rotor (specifically the permanent magnets) at any one time. Semiconductor switches, like transistors, are then used to change the electrical current through the electromagnetic windings.
As in a brushed motor, the magnetic field of the coils can be reversed on demand, by reversing the direction of current within them. They can also be turned off completely by simply denying the coil any electrical current (for example: switching it off).
Rotation of the shaft can also be controlled by adjusting the magnitude of the current in the coils.
Brushless DC motors, like brushed ones, are used almost ubiquitously today. Because of their high efficiency and controllability, not to mention longer lifespan, they tend to be found in devices that either run continuously or are in regular use.
They can be found in, for example, washing machines, air conditioners, electrical fans, and other consumer electronics. Because of the way they work they have contributed to a significant reduction in the power consumption of many modern electronic devices.
Electric vehicles and drones also make good use of brushless motors, due to their ability to deliver precision control. This is essential, as drones need to constantly, and precisely, control the speed of each rotor to perform actions like hovering.
You can also find them in vacuum machines, and were formerly used to spin hard disc drives in older computers. They are also widely used in computer fan assemblies.
The durability and operating dependability over the long-term, as well as energy efficiency and high output power to size ratio , is fast making them the motor of choice for many electronics in development today.
For this reason, it is expected that brushless motors will find increasingly wider applications. They will likely, for example, likely be a common feature of service robots, as brushless motors are better suited to controlling force than other alternatives like stepper motors.
By now, you should have an appreciation for the difference between the two types of motors. Given their differing designs, there are some other inherent benefits of one over the other.
These include, but are not limited to:
And that, as they say, is a wrap.
We hope you now have an understanding of the two types of motors and the basic principles that underlie their design. You should also now have an appreciation for the relative pros and cons of either device.
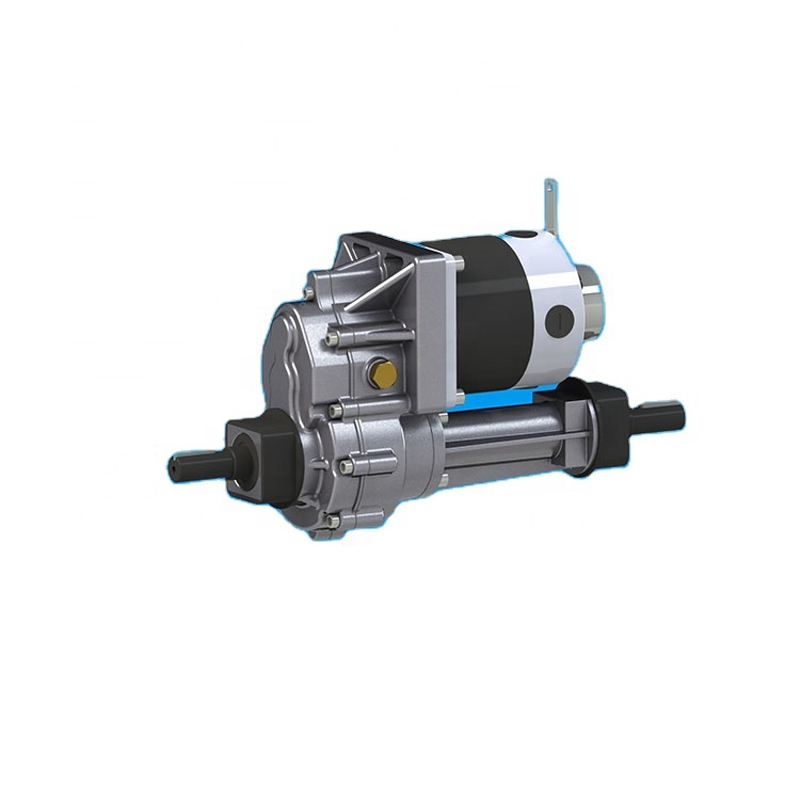
Classes Of Electric Motors So next time you are considering grabbing yourself a power tool or motor for your next project, you might want to consider forking out a little bit more for a brushless one?